Резюме:
В этом исследовании был представлен метод радиальной кристаллизационной очистки под индукцией для получения затравочных кристаллов 6N, 7N сверхвысокой чистоты. Было исследовано влияние температуры охлаждения на морфологию затравочного кристалла, а также температуры охлаждающей воды, скорости потока и количества добавляемого затравочного кристалла на процесс кристаллизации, и были получены следующие наилучшие параметры процесса очистки: температура приготовления затравочного кристалла: 278 К; Температура и расход охлаждающей воды 293 К и 40 л · ч-1; а количество семян добавил шесть.
Было исследовано влияние температуры и потока охлаждающей воды на скорость кристаллизации. Скорость кристаллизации линейно уменьшалась с увеличением температуры охлаждающей воды, но экспоненциально увеличивалась с увеличением потока охлаждающей воды. Соответствующее уравнение для скорости кристаллизации было определено экспериментально, и были предложены три схемы очистки. Когда неочищенный галлий 4 N очищали в соответствии со схемой I, галлий 6 N высокой чистоты и галлий 7 N высокой чистоты получали в соответствии со схемами II и III. Чистота галлия высокой чистоты, полученного на трех схемах I, II и III, составляла 99,999987%, 99,9999958% и 99,9999958% соответственно.
1. введение
В 1970-х годах было обнаружено, что соединения, содержащие галлий и элементы группы IIIA, обладают превосходными полупроводниковыми свойствами. С тех пор галлий (Ga) постепенно стал использоваться в качестве сырья в полупроводниковой промышленности. В последние годы, с непрерывным развитием науки и технологий и стремлением людей к низкоуглеродной экономике и зеленой энергии, применение Ga было полностью развито и стало одним из наиболее важных сырьевых материалов в области современных полупроводников (около 80%). от общего потребления галлия), солнечной энергии (около 10% от общего потребления галлия), магнитных материалов (около 5% от общего потребления галлия) и катализаторов, которые широко используются в оборонной промышленности, волоконно-оптической связи, аэрокосмической и других областях. В настоящее время технология производства галлия низкого качества (чистота ≤ 99,99%) ежедневно совершенствуется. Статистические данные Геологической службы США (USGS) за 2018 год показывают, что объем производства низкосортного первичного галлия во всем мире составил ~ 2017 тонн в 315 году, что на 15% больше, чем в 2016 году, когда он составлял 274 тонны. Спрос на галлий высокой чистоты увеличился с разработкой высокоэффективных полупроводниковых устройств, поскольку даже очень небольшие количества примесей, таких как Cu, Pb, Fe, Mg, Zn и Cr, присутствуют в потоке, крупномасштабный промышленный галлий может ухудшить или ухудшить электрические свойства. ограничить. Использовались обычные методы очистки, такие как электролитическая очистка, региональная плавка, вакуумная перегонка и метод вытягивания монокристаллов.
Для производства галлия высокой чистоты процесс электролитического рафинирования в настоящее время является наиболее широко используемой технологией в промышленности для производства галлия высокой чистоты. Однако у этих традиционных методов было много проблем, таких как высокое энергопотребление, отсутствие экологичности, низкая эффективность производства и неудобное автоматизированное управление. Поэтому разработка передовых технологий очистки очень важна для развития современной полупроводниковой и солнечной промышленности. Очистка и рафинирование галлия нами систематически исследовались. На основе обычного способа кристаллизации был предложен способ получения кристаллизующихся кристаллов, индуцированных кристаллизацией с затравочными кристаллами. Процесс имеет преимущества низкого потребления энергии, простого оборудования, удобного управления и короткого производственного цикла. В этом исследовании эксперимент по кристаллизации использовался для исследования влияния температуры охлаждения на морфологию кристалла и влияние температуры охлаждающей воды, скорости потока и количества затравочных кристаллов, добавленных в процессе кристаллизации. Параметры процесса очистки были изучены с целью оптимизации наилучшего процесса очистки, определения уравнения регулирования скорости кристаллизации и получения металлического галлия высокой чистоты (6N и 7N) в условиях процесса.
2. Материалы и методы
2.1. Схема технологического процесса 1 показывает процесс производства высокочистого бициклического кристалла галлия 6N, 7N путем индукции затравки. Основные этапы и процедуры заключаются в следующем: (1) Очистка кристаллизатора и сборка очистителя. Сначала кристаллизатор промыли водой высокой чистоты (удельное сопротивление ≥ 16 МОм · см), чтобы удалить пыль с поверхности. Затем его очищали ультразвуковым очистителем, содержащим сверхчистую воду, в течение часов 2, чтобы удалить остаточные загрязнения с поверхности. Устройство очистки было собрано, как показано в 1b. (2) Предварительная обработка 4 N необработанного галлия. Неочищенный галлий 4 N помещали на конфорку вместе с упаковочной бутылкой, и температуру нагрева устанавливали на 335 K. После того как галлий расплавился, расплавленный сырой галлий перенесли в стакан из политетрафторэтилена и смешали с 200 мл 3 моль / л HCl при 335 K в течение 2 часов. Соляную кислоту отсасывали пластиковой пипеткой, а затем 200 мл 3 моль / л HNO & sub3; добавлен в химический стакан с последующим перемешиванием и перемешиванием в течение 2 часов. Неочищенный галлий промывали кислотой, а затем трижды промывали сверхчистой водой. Все хлористоводородная и азотная кислоты, использованные при кислотной обработке, были высокой чистоты, и для приготовления раствора кислоты использовалась сверхчистая вода. Предварительно обработанный расплавленный сырой галлий (4 н.) Переносили в чистый кристаллизатор. В водяную рубашку кристаллизатора вводили циркулирующую охлаждающую воду. Охлаждающая вода подавалась с использованием водяного бака с низкой постоянной температурой и встроенного циркуляционного насоса. Диапазон температур составлял от 263 до 373 К, точность регулирования температуры составляла ± 0,1 К, а расход охлаждающей воды контролировался расходомером со стеклянным ротором. Когда температура жидкого галлия упала до критической точки кристаллизации, были добавлены затравки кристаллов и циркулировала охлаждающая вода. Эти кристаллы были приготовлены с использованием галлия 7N в качестве исходного материала для начала теста очистки. Используемая процедура является следующей: чашка из политетрафторэтилена, содержащая расплавленный галлий 7N, была нагрета до низкой постоянной температуры для охлаждения и кристаллизации воды. Жидкий галлий непрерывно перемешивали с помощью тефлонового стержня, чтобы диспергировать кристаллическое ядро и улучшить скорость нуклеации. В процессе перемешивания наблюдалась кристаллизация жидкого галлия.
Был включен трехходовой переключатель, и циркулирующая горячая вода была введена в зону охлаждения / плавления кристаллизатора. После того, как твердый галлий был полностью расплавлен, трехходовой переключатель перевернулся, и циркулирующая охлаждающая вода снова была введена в зону охлаждения / плавления; Подача горячей воды осуществлялась из резервуара с постоянной температурой воды и встроенного циркуляционного насоса. Диапазон температур составлял 278–373 К, а точность контроля температуры составляла ± 1 К. Этапы (как показано на рисунке 1c) повторялись до определенного числа кристаллизации. После завершения очистки было определено качество продукта.
Трехпозиционный переключатель был включен, и циркулирующая горячая вода была введена в зону охлаждения / плавления кристаллизатора. После того как твердый галлий был полностью расплавлен, трехходовой переключатель был переключен, и циркулирующая охлаждающая вода была снова введена в зону охлаждения / плавления; Горячая вода подавалась с использованием водяного бака постоянной температуры и встроенного циркуляционного насоса. Диапазон температур был 278-373 K, а точность контроля температуры была ± 1 K.
Шаги (как показано на рисунке 1c) повторяли до заданного количества кристаллизаций. После завершения очистки определялось качество продукта.
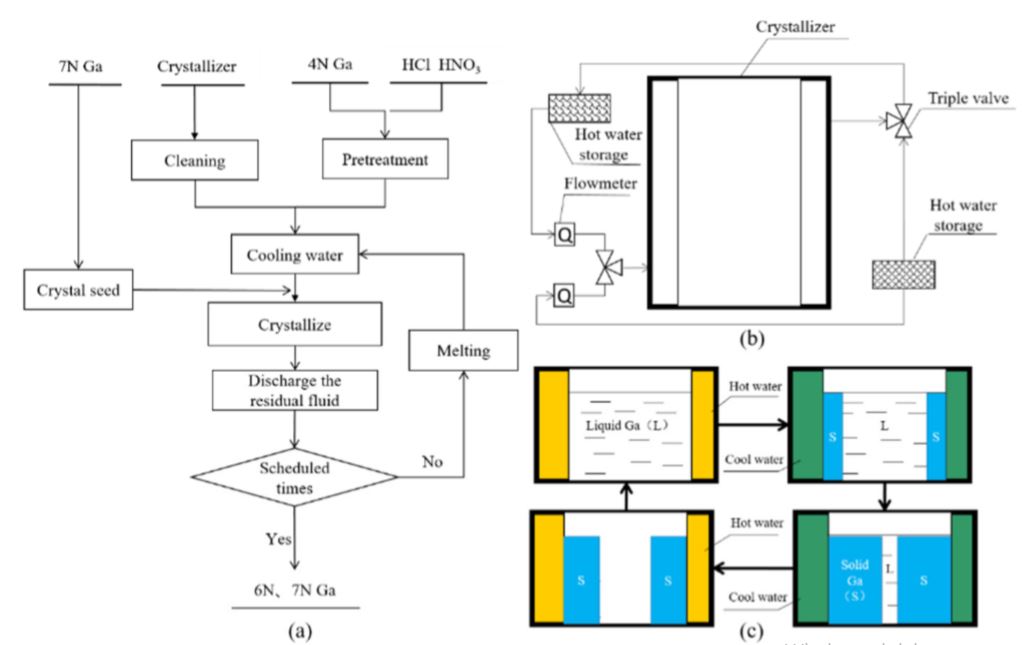
Рисунок 1. Схематическое представление процесса очистки: (a) последовательность процессов для очистки, (b) сборка устройства для очистки и (c) повторный процесс кристаллизации.
2.2. методы обнаружения
В эксперименте содержание примесей в галлиевом сырье 4N и очищенном галлии 6N, 7N детектировали с помощью масс-спектрометрии с тлеющим разрядом высокого разрешения (Evans Materials Technology (Shanghai) Co., China, HR-GDMS)), а чистоту продукта определяли разностным методом. рассчитывается. Аргон был использован в качестве газа обнаружения. Параметры масс-спектрометрии следующие: ток разряда 1,9 мА; Напряжение разряда 1 кВ; Лучевой ток иона галлия 1 × 10-6 мА; Изоляционный слой, алюминий; и разрешение ≥ 3600. Перед сбором данных источник ионов HR-GDMS охлаждали до температуры жидкого азота (90 K), чтобы уменьшить влияние ионов в фоновом газе. Затем поверхность испытуемого образца (0,2 x 2 мм 2) распыляли в течение минут 5 при температуре жидкого азота для удаления загрязнений с поверхности образца. Условия до распыления были постоянными, и сбор данных был начат. В процессе сбора данных время интеграции было установлено равным 80 мс.
3. Результаты и обсуждение
3.1. Влияние температуры охлаждения на морфологию семян
Морфология внешнего вида затравочного кристалла, полученного при температуре охлаждения в диапазоне 265-295 K, показана на рисунке 2. Это показывает, что затвердевшая структура в 265 K содержала много мелкокристаллических зерен, и зерна перемежались большим количеством жидкого галлия. Когда отвержденная структура была удалена, большое количество жидкого галлия связывалось с поверхностью, что приводило к крайне неправильной форме затравки, поскольку в 265 K скорость роста кристаллического ядра после нуклеации увеличивалась из-за высокой степени переохлаждения, что приводило к образованию кристаллического ядра. большое количество дендритов приводит. Быстрый рост дендритов не только смешивается с большим количеством жидкой фазы в затвердевшей структуре, но также вызывает много полой поверхности затвердевшей структуры. При температуре приготовления 273 K затвердевшая структура показала особенности геометрической многогранной формы, что указывало на то, что с уменьшением степени переохлаждения скорость роста кристаллического ядра снижалась, и его режим роста переключался с роста дендритов на рост пластинчатых. Когда температура производства составляла 278 K, затвердевшая структура имела правильную гексаэдральную форму, что указывало на то, что с ростом температуры степень переохлаждения фронта роста после образования кристаллического ядра продолжала уменьшаться, а режим роста изменялся с точки зрения роста в слоях. При температуре приготовления 295 K степень переохлаждения границы раздела твердое тело-жидкость дополнительно снижалась после образования кристаллического ядра, предотвращая выделение скрытой теплоты при кристаллизации. В это время направление роста кристаллического ядра изменилось на боковой, искажая его геометрическую форму, чтобы быстрее высвободить скрытую теплоту кристаллизации. Путем сравнения морфологических свойств затравок, полученных при четырех температурах, оптимальная температура получения затравочного кристалла была окончательно определена как 278 К. При температуре производства 273 К затвердевшая структура проявляла особенности геометрической многогранной формы, что указывает на то, что по мере уменьшения степени переохлаждения скорость роста кристаллического ядра уменьшалась, и режим его роста изменялся с роста дендритов на рост ламелей. Когда температура производства составляла 278 K, затвердевшая структура показала правильную гексаэдральную форму, что указывает на то, что с увеличением температуры степень переохлаждения фронта роста после образования кристаллического ядра продолжала уменьшаться, а режим роста переходил в рост вертикального слоя. При температуре приготовления 295 K степень переохлаждения границы раздела твердое тело-жидкость дополнительно снижалась после образования кристаллического ядра, предотвращая выделение скрытой теплоты при кристаллизации. В это время направление роста кристаллического ядра изменилось на боковой, искажая его геометрическую форму, чтобы быстрее высвободить скрытую теплоту кристаллизации.
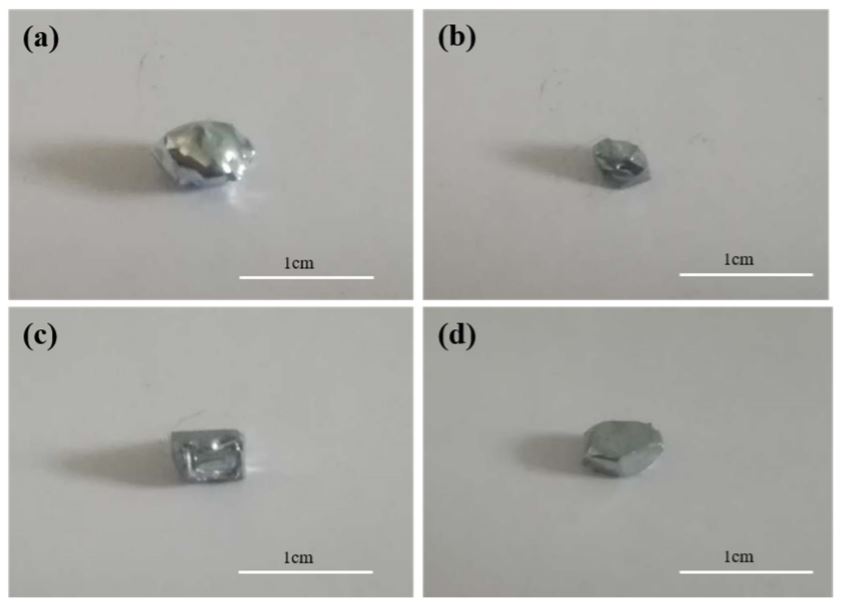
Рисунок 2. Морфология затравочных кристаллов, полученных при различных температурах охлаждения ((a) 265 K, (b) 273 K, (c) 278 K и (d) 295 K).
3.2. Влияние параметров процесса на процесс кристаллизации
3.2.1. Влияние температуры охлаждающей воды на процесс кристаллизации
Когда скорость потока охлаждающей воды составляла 40 L · h-1 и температура находилась в диапазоне 288-298 K, 2,9774 кг необработанного галлия, предварительно обработанного травлением, охлаждали до критической точки кристаллизации с последующим добавлением затравки для 15. минут Соответствующая морфология роста кристаллов показана на рисунке 3.
На рисунке 3 показано, что когда температура охлаждающей воды была 288 и 290 K, режим роста жидких кристаллов галлия был в основном ростом дендритов после добавления затравочного кристалла, и ветви кристаллов были соединены друг с другом, при этом жидкий галлий оказался в кристалле. Это было связано с тем, что при более низкой температуре охлаждающей воды градиент температуры внутри жидкого галлия был выше, а скорость роста кристалла после добавления затравочного кристалла была выше. Хотя в это время формировался положительный температурный градиент, температура на фронте границы раздела твердое тело-жидкость в радиальном направлении кристаллизатора была выше, что предотвращало выделение скрытой теплоты кристаллизации в этом направлении и, таким образом, уменьшало рост кристаллов в этом направлении. Однако, чтобы облегчить выделение скрытой теплоты кристаллизации, ориентация роста кристалла изменилась и быстро выросла в виде дендритов, в конечном итоге разрушая ветви кристаллов и перекрывая
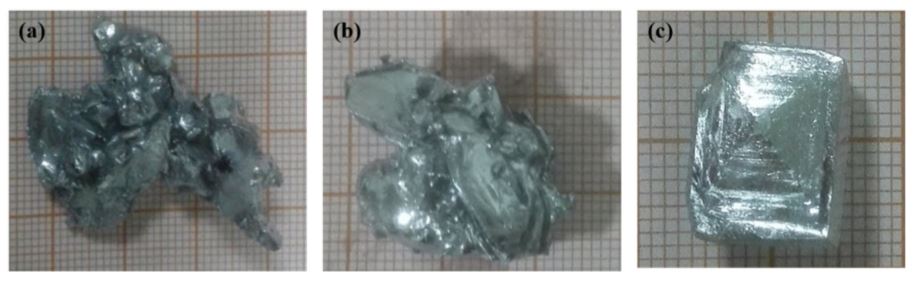
Рисунок 3. Кристаллическая морфология жидкого галлия после 15-минутного добавления ядер при различных температурах охлаждающей воды ((a) 288 K, (b) 290 K и (c) 293 K).
Включение жидкой фазы.
Увлеченные жидкофазные загрязнения не могут быть удалены из-за роста кристаллов, что влияет на процесс очистки. Когда температура охлаждающей воды была 293 K, после добавления затравочных кристаллов жидкий галлий вырос до монокристалла.
Чтобы дополнительно проанализировать закон роста жидкого галлия во время кристаллизации, морфологию кристалла исследовали в различные моменты времени после добавления ядер кристаллов методом динамического измерения времени при потоке охлаждающей воды 40 L · h-1 и температуре 293 K. Результат показано на рисунке 4.
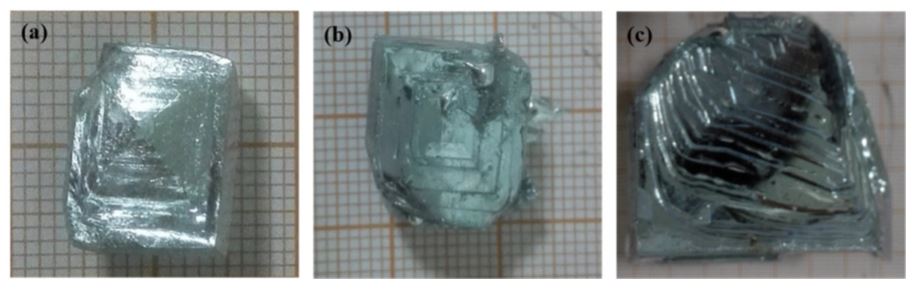
Рисунок 4. Морфологические изображения кристаллических блоков в разное время после добавления затравки ((a) 15 min, (b) 30 min и (c) 60 min).
На рисунке 4 показано, что после добавления затравки слиток кристаллов галлия постепенно увеличивался с увеличением времени кристаллизации, а режим роста жидких кристаллов галлия после добавления затравочных кристаллов показал типичный многослойный рост сдвига, указывающий температуру. Градиентная среда, образованная охлаждающей водой при 293 K, могла бы быть В результате роста кристаллов образуется скрытая теплота кристаллизации к фронту границы раздела твердое тело-жидкость, и они переносятся и выпускаются вдоль направления градиента температуры наружу. Этот тип роста кристаллов в слоях был выгоден для накопления примесных элементов от границы раздела твердое тело-жидкость к жидкой фазе, тем самым получая металлический Ga с более высоким содержанием Ga. Степень переохлаждения пика роста была наибольшей, когда кристалл рос, и атомы жидкого галлия на границе раздела твердое тело-жидкость были преимущественно связаны на пике роста, и тепло передавалось наружу от кристаллизованного твердого галлия к положительному градиенту температуры в кристаллизаторе. , Поэтому рост кристаллов в процессе кристаллизации всегда был в форме пирамидального ступенчатого развития. В соответствии с кинетикой и термодинамикой роста кристаллов слоистый рост оказался способствующим увеличению площади поверхности кристаллов, способствуя выделению скрытой теплоты кристаллизации и обеспечивая непрерывный и устойчивый рост кристаллов в процессе кристаллизации. Кроме того, согласно теории разделения и коагуляции примесей в кристалле можно предположить
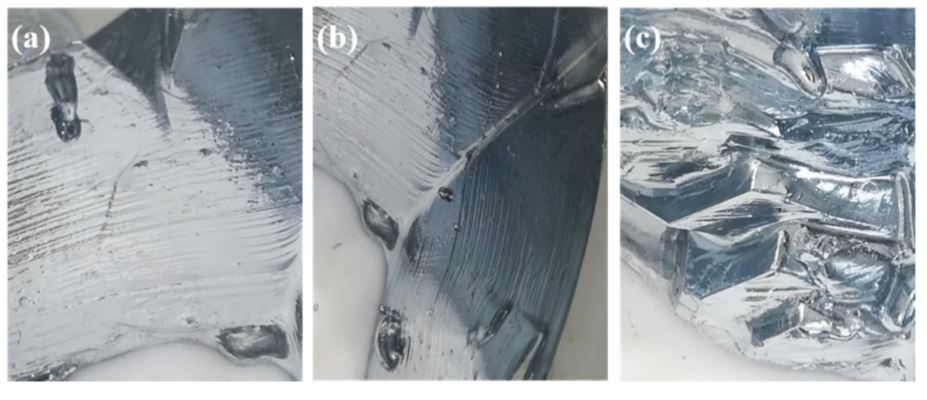
Рисунок 5. (a) Для 30 L · h · 1 около выхода из кристаллизатора, (b) для 40 L · h · 1 возле входа в кристаллизатор и (c) для 50 L · h · 1 - детальная морфология кристалла галлия возле входа в кристаллизатор кристаллизатор чистого прохода.
Обогащение примесных элементов от границы твердое тело-жидкость до жидкого состояния и уклонение примесей оболочками жидкой фазы из-за неправильного направления роста кристаллов. 4 показывает, что с увеличением времени кристаллизации острие пирамиды кристалла становилось все более очевидным, и этап наслоения роста кристалла становился все более очевидным, поскольку кристаллизация продолжалась, примесные элементы постоянно накапливались в жидкой фазе, и чистота увеличивалась на границе раздела твердое тело-жидкость. что способность к сцеплению поверхности раздела твердое тело-жидкость улучшало пик роста кристаллов. Из-за разницы в атомном радиусе и электроотрицательности между Ga и примесными элементами примесные атомы, прикрепленные к пику роста, проникали в решетку Ga или в вакансию решетки и вызывали дефект роста кристалла Ga. Это показало, что удаление примесных элементов уменьшалось с ходом кристаллизации и совпадало с литературными данными.
3.2.2. Влияние потока охлаждающей воды на процесс кристаллизации
В предыдущем исследовании, прежде всего, было исследовано влияние потока охлаждающей воды на процесс кристаллизации. Результаты показали, что скорость роста кристалла галлия вблизи выходного отверстия кристаллизатора была несколько ниже, чем в других регионах, когда скорость потока охлаждающей воды была 30 L · h-1. Когда скорость потока охлаждающей воды была 50 · H-1, скорость роста кристалла галлия в нижней части кристаллизатора была немного больше, чем в верхней части, и скорость роста у входа в кристаллизатор была наибольшей. При скорости потока охлаждающей воды 40 L · h-1 скорость роста кристаллов галлия была практически одинаковой во всех областях кристаллизатора, и ни одно локальное явление роста не наблюдалось слишком быстро или слишком медленно. Для дальнейшего исследования влияния этого параметра процесса на процесс кристаллизации была обнаружена морфология кристалла жидкого галлия при различных потоках охлаждающей воды. Результаты показаны на рисунке 5.
Это объясняется тем фактом, что по мере кристаллизации загрязняющие вещества непрерывно накапливались в жидкой фазе, и содержание примесей на границе раздела твердое тело-жидкость увеличивалось, увеличивая вероятность того, что загрязняющие элементы прикреплялись к пику роста кристаллов. Из-за разницы в атомном радиусе и электроотрицательности между Ga и примесными элементами примесные атомы, прикрепленные к пику роста, проникали в решетку Ga или в вакансию решетки и вызывали дефект роста кристалла Ga. Это указывает на то, что удаление примесных элементов уменьшается с развитием кристаллизации и соответствует литературным данным.
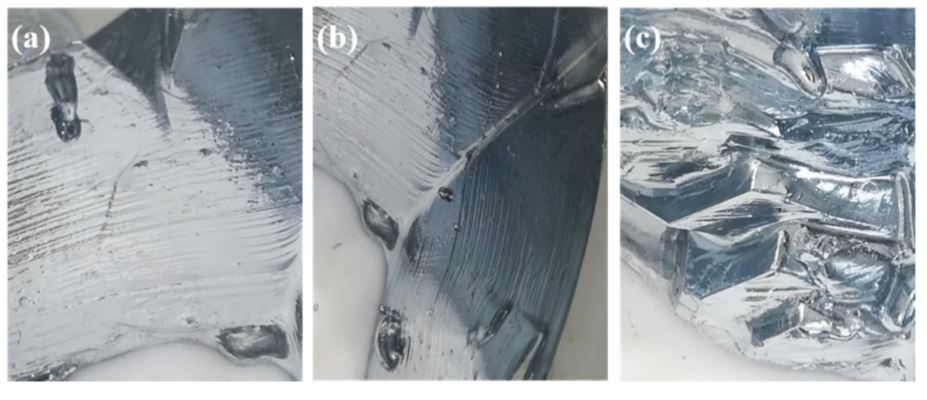
Рисунок 5. (a) Для 30 L · h · 1 около выхода из кристаллизатора, (b) для 40 L · h · 1 возле входа в кристаллизатор и (c) для 50 L · h · 1 - детальная морфология кристалла галлия возле входа в кристаллизатор кристаллизатор чистого прохода.
На рис. 5 показано, что морфология кристаллов галлия при расходе охлаждающей воды 40 л · ч - 1 демонстрирует четкую «оболочку» с равномерным расстоянием между зернами. Это указывало на то, что кристалл галлия рос слой за слоем при этой скорости потока и был полезен для удаления загрязнения. При потоке охлаждающей воды 30 л · ч - 1 скорость роста кристаллов на выходной стороне кристаллизатора была немного медленнее, чем на других участках, и морфология кристаллов была такой же, как при потоке охлаждающей воды 40 л · ч - 1, с другой отображаемой «структурой оболочки». . Это указывает на то, что в этих условиях потока кристаллы галлия также растут слой за слоем, что способствует удалению примесей; Скорость роста кристаллов здесь была ниже, чем в окружающей области, так что на данном этапе нельзя исключать возможность охвата жидкой фазы по мере продвижения кристаллизации. Однако при расходе охлаждающей воды
Рост кристаллов был больше, а скорость роста кристаллов была выше, что изменило морфологию кристаллов и наличие большого количества нерегулярных стадий роста. Из этого можно сделать вывод, что кристаллы в этом месте не выращиваются полностью в слоях, и процесс роста кристаллов может сопровождаться дендритным или перитектическим образованием, что приводит к образованию жидкой оболочки, в том числе примесей, и снижению степени очистки твердого галлия.
3.2.3. Влияние количества микробов на процесс кристаллизации
При потоке охлаждающей воды 40 lh-1 и температуре 293 K добавляли жидкий галлий, охлажденный до критической точки кристаллизации, и добавляли затравочные кристаллы 3, 4, 5 и 6. Когда кристаллизация достигла определенного уровня, ее морфологическое изображение отображается в 6, указывая на то, что количество добавленных семян определяет форму некристаллизованной области. При добавлении трех затравочных кристаллов некристаллизованная область имела треугольную форму. При добавлении четырех ядер некристаллизованная область имела равностороннюю форму. Однако, когда количество добавленных кристаллических ядер составляло 3 или 4, форма и размер некристаллизованной области не совпадали и имели форму воронки с большим верхом и небольшим дном. Это легко привело к точке пересечения роста кристаллов в нижней части кристаллизатора с непрерывным прогрессом кристаллизации, что вызвало развитие жидкой фазы и включение примесей, тем самым влияя на эффект дефлаграции. Когда было добавлено пять затравочных кристаллов, некристаллизованная область показала пятиугольную форму, и проблема формы с большой верхней и небольшой нижней частями в некристаллизованной области улучшилась. В случае добавления шести затравочных кристаллов некристаллизованная область имела гексагональную форму правильной формы и однородного размера и была наиболее предпочтительной для контроля общего направления кристалла во время очистки неочищенного галлия. Поэтому было определено, что оптимальное количество добавлений в семена составляет шесть, когда исходный галлий 4 N очищают с использованием самодельного кристаллизатора.
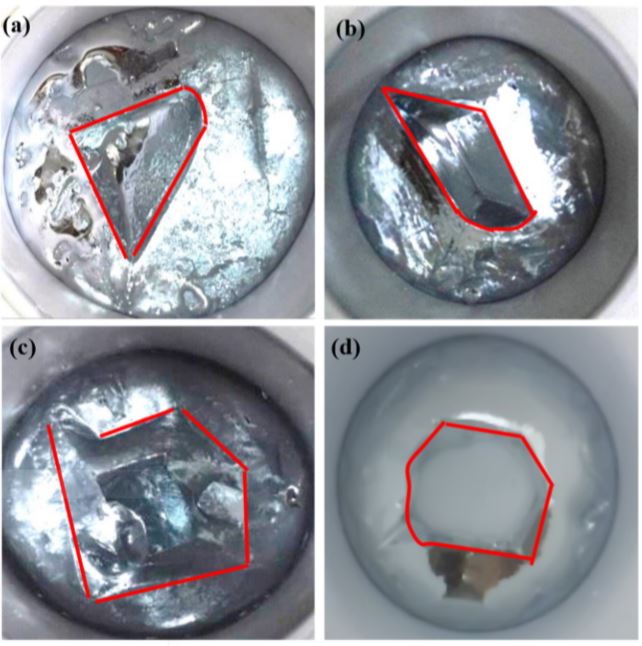
Рисунок 6. Фотографии морфологии кристаллов с добавлением различного числа ядер ((a) 3, (b) 4, (c) 5 и (d) 6).
3.3. Влияние параметров процесса
3.3. Влияние параметров процесса на скорость кристаллизации
В реальном процессе кристаллизации кристаллизации жидкого галлия скорость кристаллизации (то есть скорость роста кристаллов галлия при добавлении зародышей) зависела от степени переохлаждения границы раздела твердое тело-жидкость. Степень переохлаждения границы раздела твердое тело-жидкость была функцией температуры и потока охлаждающей воды, чтобы поддерживать другие условия процесса постоянными. В эксперименте зависимости между скоростью кристаллизации и температурой охлаждающей воды и расходом измеряли методом контрольных переменных, а эмпирическую контрольную формулу скорости кристаллизации получали путем анализа экспериментальных данных. Чтобы уменьшить погрешность эксперимента, повысить точность формулы эмпирического контроля и ее адаптивность к фактическому производственному процессу, каждую группу экспериментов по измерению повторяли четыре раза и получали среднее значение. Скорость кристаллизации, измеренная в эксперименте, была изменена во время полного процесса затвердевания жидкого галлия после добавления затравки, и формула расчета следующая:
v = м / т
где v - средняя скорость, кг / час; m - общая масса жидкого галлия, кг; t - время, необходимое для полного затвердевания жидкого галлия, час (ч). Влияние температуры и скорости потока охлаждающей воды на скорость кристаллизации, определенную в ходе испытания, показано в 7. 7a показывает, что с увеличением температуры охлаждающей воды скорость кристаллизации постепенно снижается, и между ними наблюдается очевидная линейная зависимость. Эмпирическая формула контроля температуры охлаждающей воды для скорости кристаллизации была получена с помощью программного обеспечения Origin.
v (T) = -0,09 T + 27
где Т - температура охлаждающей воды К; и коэффициент линейной корреляции данных был R2 = 0,997. 7b показывает, что с увеличением скорости потока охлаждающей воды скорость кристаллизации увеличивается, и наблюдается значительная экспоненциальная функциональная взаимосвязь между ними. Эмпирическая формула контроля потока охлаждающей воды к скорости кристаллизации была получена с помощью программного обеспечения Origin.
v (Q) = -96,73e - Q 4,94 + 0,66
где Q - расход охлаждающей воды, л / ч; и стандартное отклонение соответствия данных было R2 = 0,997.
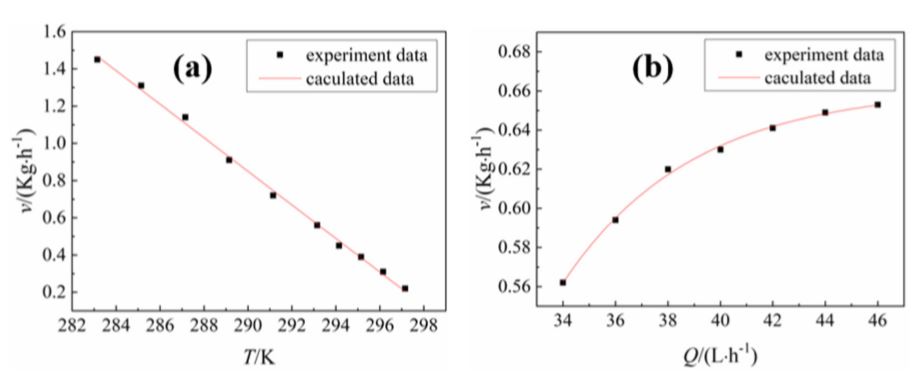
Рисунок 7. (а) Влияние температуры охлаждающей воды на скорость кристаллизации при скорости потока 40 L · h-1; (b) Влияние скорости потока охлаждающей воды на скорость кристаллизации в 293 K.
3.4. Анализ результатов очистки
На основании проведенных исследований были определены следующие оптимальные технологические параметры кристаллической очистки исходного галлия 4N: температура затравочного приготовления 278 К; Температура охлаждающей воды 293 К, расход охлаждающей воды 40 л · ч-1, и количество добавленных затравочных кристаллов составляло шесть. В сочетании с нашим предыдущим исследованием были созданы три схемы очистки.
Уровни примесей в галлии высокой чистоты, полученном по трем схемам очистки, были протестированы и сравнены с сырьем галлия, и была рассчитана скорость удаления примесей. Результаты показаны в таблице 2.
Таблица 2 показывает, что после очистки фракции примесей, содержащихся в материалах, были снижены ниже предела обнаружения HR-GDMS, а остальные шесть основных примесей также были хорошо удалены. Степени удаления были следующими: Fe-87,1%, Pb-95,9%, Zn-89,9%, Mg-97,9%, Cu-98,8% и Cr-93,3%, а массовая доля металла алюминия, рассчитанная по разностному методу, составляла 99,999987%.
Для схемы II скорости удаления шести основных примесей составляли Fe-93,8%, Pb-98,8%, Zn-95,6%, Mg-99,6%, Cu-99,8% и Cr-97,6%, а массовая доля основного металла Ga составляла 99,9999958%. , Для схемы III скорости удаления шести основных примесей продолжали увеличиваться, и скорости удаления Mg и Cu превышали 99,9%. Напротив, степень удаления железа, хотя и самая низкая, также достигла 97%. Массовая доля основного металла Ga составляла 99,9999958%.
4. выводы
Таким образом, предлагается детально устранить примесь исследуемого Ga и выполнить процесс очистки кристаллизации с использованием этой индукции кристалла. Влияние температуры охлаждения на морфологию кристалла, а также на температуру охлаждающей воды, скорость потока и количество ядер, добавленных в исследуемый процесс кристаллизации. Был получен оптимальный метод очистки; определено контрольное уравнение скорости кристаллизации; и галлий высокой чистоты (6N и 7N) был получен в технологических условиях. Основные выводы этого исследования заключаются в следующем:
- Оптимальные параметры процесса для кристаллизационной очистки сырья 4N галлия следующие: температура подготовки семян 278 K; Температура охлаждающей воды 293 K; Расход охлаждающей воды 40 L · h - 1; количество затравочных кристаллов добавлено шесть 6;
- Скорость кристаллизации линейно уменьшалась с увеличением температуры охлаждающей воды и экспоненциально возрастала с увеличением потока охлаждающей воды. Управляющие формулы температуры охлаждающей воды T и скорости потока Q по скорости кристаллизации v: v (T) = -0,09T + 27 и v (Q) = -96,73e -Q 4,94 + 0,66;
- Три предложенные схемы очистки эффективно удаляют загрязняющие элементы. При использовании схемы I для очистки неочищенного никеля 4 был получен галлий высокой чистоты с чистотой 6 N. Используя схемы II и III, 7N был получен для галлия высокой чистоты. Чистота галлия высокой чистоты, полученного по схемам I, II и III, составляла 99,999987%, 99,9999958% и 99,9999958% соответственно.
Метод, предложенный в исследовании для радиальной кристаллизации, вызванной затравкой, предлагает преимущества простоты эксплуатации, удобного технологического процесса, низкого энергопотребления, экологически чистого и простого в применении автоматического управления процессом очистки и дает новую идею для крупномасштабного промышленного производства галлия высокой чистоты. ,
Институт редкоземельных металлов
Кафедра химии и химического машиностроения, Университет Ллянлян, Китай
Школа металлургии, Северо-восточный университет, Шэньян, Китай